Since 2014, HITCHINER Manufacturing has been supplying extraordinary and highly complex castings for turbochargers without a single defect! An unparalleled result, distinguished with the Daimler Supplier Award 2018 in the category of Quality (Global Procurement Trucks & Buses).
The engines in modern Daimler Trucks develop their full power output through the use of turbochargers. Charging the engine with air or the vehicle’s own exhaust gas recirculation system increases torque and power enormously.
These high-precision turbochargers represent the right mix between maximum power gain and high running output stability. This is crucial because a Daimler truck must reliably draw sufficient power from the lower rpm ranges at all times, and must do so over the entire useful life of the engine.
Turbochargers and their housings are subjected to extreme demands in daily use. It is important that the individual components manufactured from castings, be of the highest quality. The US company HITCHINER Manufacturing Co., Inc. fulfilled this requirement 100% of the time.
Five years – zero defects!
Since 2014, HITCHINER Manufacturing has been supplying extraordinary and highly complex castings for turbochargers without a single defect! An unparalleled result, distinguished with the #Daimler Supplier Award 2018 in the category of Quality (#Global Procurement Trucks & Buses). HITCHINER has thus not only made it onto the winner’s podium of the Supplier Awards. With this 0 defect result, HITCHINER has made a decisive contribution to the proverbial reliability of Daimler Trucks & Buses.
Founded in 1946, with its headquarters in Milford, New Hampshire and further offices in the USA and Mexico, the company is a highly sought-after partner worldwide, mainly by automotive and aerospace companies. HITCHINER has a staff of 1800 employees. The production of high-quality precision castings is part of its core business. HITCHINER achieves the sensational zero defects rate through a patented manufacturing technology. Special vacuum processes make it possible to form very thin wall parts with maximum strength.
" For five consecutive years, Hitchiner Manufacturing has been delivering consistently outstanding and highly complex castings for turbochargers to Daimler Trucks. Since 2014, our partner simply delivered, casting the quality standard in one of a kind quality trucks. "
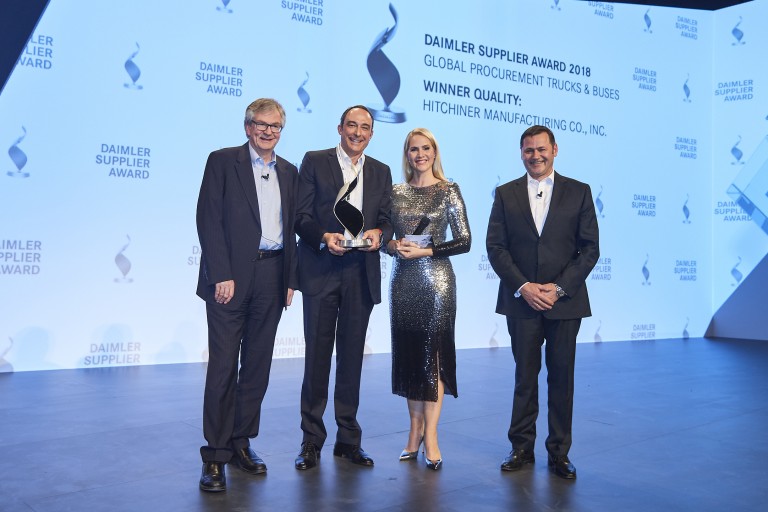
Three questions for HITCHINER Chairman & CEO John Morison
Congratulations Mr. Morison. Your company was awarded the Daimler Supplier Award 2018 in the Quality category by Global Procurement Trucks & Buses. We are pleased about your success and would like to ask you three questions:
1. What is your general secret to success?
We use a HITCHINER developed counter gravity centrifugal casting version of the centuries old lost wax casting process to produce high temperature turbine wheels for Daimler turbochargers. Establishing optimal process parameters and controlling process variables for each of the four key process steps (wax injection, ceramic mold manufacture, melting and casting, and finally metal finishing and thermal processing), are critical to the manufacture of parts that meet the stringent Daimler specification.
2. How does one achieve a zero error result 5 years long?
The easy answer is to follow the established process without deviation. Actually, we are constantly working to develop a better understanding of each of the critical process steps in order to improve casting quality and to reduce and ultimately eliminate process variability.
3. How did your team receive the Award?
We were surprised, ecstatic, and thrilled. Our goal, since we started this relationship with Daimler in 2013, was to become Daimler’s supplier of choice for these castings. This award serves as recognition of our achievement. Our goal for the next five years is to continue to improve our process in order to improve the quality of the parts we produce and to reaffirm Daimler’s confidence in HITCHINER as a supplier.
We thank you for the answers and congratulate you and your team for the achievement and the well-deserved award.
Note: This articles was originally published on May 13, 2019 on the previous Daimler Supplier Magazine Online platform.